Digitalización con estándares abiertos: la receta para dormir bien
Publicado a las 02 de septiembre de 2024 el Operational Excellence
Estas son algunas de las preocupaciones que quitan el sueño a los directores de fábrica; preocupaciones que pueden abordarse mediante la digitalización. En un entorno de producción digitalizado, los directores de fábrica no tienen que preocuparse por las incertidumbres, los riesgos y los "podría pasar". La digitalización elimina la incertidumbre y permite una optimización basada en el rendimiento. Proporciona información que puede ayudar a los directores de fábrica a mejorar la calidad, reducir los costes, acortar los plazos de entrega y reducir el impacto medioambiental. El director de una fábrica digitalizada no debería despertarse preocupado en mitad de la noche, pero si lo hace, un breve vistazo a su teléfono móvil debería tranquilizarle y asegurarle que todo funciona como debería.
Sin embargo, pasar de un estado de insomnio inducido por la ansiedad a otro de feliz somnolencia no es fácil. Dicho sin rodeos, la digitalización puede ser bastante tediosa. Los jefes de proyecto rara vez tienen el lujo de trabajar con una hoja en blanco; la mayoría de las veces trabajan con una serie de retales de viejas tecnologías entrelazadas; intentan digitalizar líneas de producción que incorporan máquinas que nunca han registrado datos y que se construyeron antes de que existieran los protocolos de comunicación de datos. Todo ello supone un reto considerable para la integración de la TO y la TI.
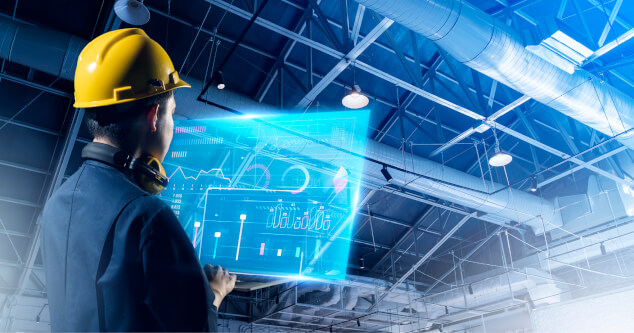
Objetivo del 80 %
Es posible utilizar estándares no abiertos, pero en última instancia esto limitará la capacidad para aprovechar plenamente las oportunidades de optimización del rendimiento que presenta la digitalización y para comunicarse más allá de las paredes de la fábrica, por lo que abogamos por un enfoque de digitalización basado en estándares abiertos.
Para recopilar datos de máquinas y procesos en tiempo real, un lenguaje de modelado común como PackML logrará la estandarización. El éxito de la digitalización también requiere un protocolo de comunicación estandarizado para que las máquinas puedan comunicarse entre sí y con otros componentes de la Industria 4.0. OPC UA, un protocolo que tiene su origen en el ámbito de la TI, se está trasladando cada vez más a la esfera de la automatización industrial, y OMRON forma parte de un comité directivo dirigido por la industria de la automatización que está ampliando OPC UA a dispositivos industriales de campo con UPC UA FX.
La analogía que suele utilizarse es con la lengua inglesa, la lengua universal de los negocios. Si habla inglés, puede hacer negocios con la mayoría de la gente. El mismo principio se aplica a OPC UA FX en un contexto industrial.
Este estándar abierto admite una interoperabilidad completa dentro de una fábrica. No solo permite a las máquinas comunicarse entre sí mediante datos, sino también con los sistemas informáticos, como los sistemas ERP y MES, así como con los sistemas de análisis de datos que se puedan estar ejecutando en una nube local o virtual.
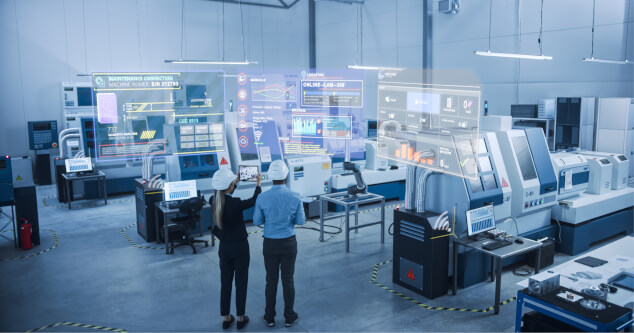
Apertura de oportunidades
La digitalización de estándares abiertos también es clave para obtener valor de los pasaportes de producto digitales (DPP). Además de ser un requisito legal a partir de 2027 para algunas industrias, los DPP, que proporcionan un registro digital de la composición, el origen y el ciclo de vida de un producto, son una herramienta muy útil de la Industria 4.0. En la producción de baterías para vehículos eléctricos, por ejemplo, los DPP podrían utilizarse para mejorar la calidad y reducir los residuos. Se ha comprobado que combinar componentes de la misma calidad da como resultado una batería mejor. La razón de que esto no ocurra siempre es la variación que se produce dentro de las tolerancias establecidas. Utilizando datos de DPP comunicados a través de OPC UA, los almacenes podrían seleccionar componentes específicos con características similares y reducir así el riesgo de que las baterías no superen las pruebas de fábrica y tengan que ser desechadas.
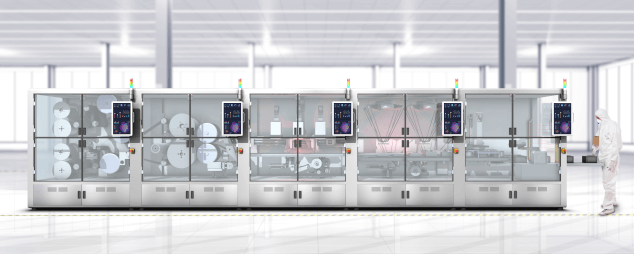
La digitalización está ganando impulso gracias a la creciente concienciación sobre los beneficios reales que pueden aportar los conocimientos basados en datos. Sin embargo, la estandarización, en cuanto al tipo de datos que se recopilan y la forma en que se comunican esos datos, es un reto importante para las fábricas que desean digitalizar la automatización industrial. Al adoptar un enfoque de estándares abiertos, los fabricantes podrán tener éxito en la digitalización y los directores de fábrica podrán dormir tranquilos.